Big Trucks Join Vehicles of all Sizes in Combating Climate Change
Across the country, companies and workers are building the advanced fuel-efficient vehicles of the future. These are not just our cars, SUVs and pickup trucks, but also “medium- and heavy-duty” vehicles—everything from super-duty pickups, work vehicles, and buses, to delivery trucks and long haul semis/tractor-trailers that move America’s packages and goods. Broad-based innovation across the industry has been essential to rebuilding a strong, globally competitive domestic transportation supply chain—and the manufacturing jobs that go with it.
Building more fuel-efficient super-duty pickups at Ford’s Kentucky Truck Plant in Louisville. Photo credit: Sam VarnHagen, Ford Motor Co.
Across the country, companies and workers are building the advanced fuel-efficient vehicles of the future. These are not just our cars, SUVs and pickup trucks, but also “medium- and heavy-duty” vehicles—everything from super-duty pickups, work vehicles, and buses, to delivery trucks and long haul semis/tractor-trailers that move America’s packages and goods.
Not only are fuel economy improvements in larger vehicles critical to meeting the nation’s climate goals, but as all types of vehicles improve, innovation to build cleaner, more fuel-efficient technology reaches into almost every manufacturing plant in the industry. This includes major car, truck, and bus assembly plants, suppliers making key subsystems, and manufacturers of components, trailers, tires, and the steel and aluminum that go into them. Broad-based innovation across the industry has been essential to rebuilding a strong, globally competitive domestic transportation supply chain—and the manufacturing jobs that go with it.
The EPA recently finalized Phase 2 fuel efficiency and greenhouse gas standards that keep fuel efficiency improving in medium- and heavy-duty trucks. At the same time, EPA and NHTSA are reviewing the rapid technological progress meeting the passenger vehicle standards. Here’s a look at how Americans are getting the job done, and what it takes to keep both the fuel savings and manufacturing job growth going.
What does building advanced medium- and heavy-duty vehicles in America looks like?
Passenger vehicle innovation pays off in super-duty work trucks
Combating Climate Change 426,000 Pickup Trucks at a Time showed that, even for passenger vehicles, saving fuel and combating climate change isn’t just about small cars. On the contrary, big improvements in fuel economy are taking place in even the largest passenger vehicles, like the Ford F-150 and Chevy Silverado, are essential to ensuring that car and truck “CAFE” standards meet climate goals and work for consumers at the same time. Now, innovation used to improve fuel economy in light trucks is resulting in benefits across the transportation sector.
Automakers, as well as steel and aluminum companies, have invested billions of dollars in innovative lightweight materials, and the new robotics, processes, and training needed to integrate lightweight fuel-saving materials into high volume passenger vehicles like the Ford F-150, manufactured at Ford’s Kansas City Assembly plant. In 2015, Ford announced a similar $1.3 billion investment—and 2,000 new jobs—at its Kentucky Truck Plant in Louisville, Kentucky. This investment allowed the company to build bigger super-duty work trucks, including the F-250, 350, and 450, with similar aluminum alloy cab and a 95 percent high strength steel box and frame, which results in increased tow and payload capability, improved acceleration, and reduced stopping distance while still cutting weight and improving fuel efficiency.
No such thing as a “conventional” vehicle
While there is exciting progress happening in electric vehicles, the majority of the big fuel efficiency gains we are seeing now and over the next decade will come from innovation in “conventional” gas and diesel internal combustion engines and transmissions, components, electronics, and materials. These high-tech diesel trucks are anything but “conventional,” however, incorporating novel technologies, configurations, and electronic controls engineered to achieve significantly greater fuel efficiency.
“…our latest technologies are already enabling our customers to reduce fuel consumption and emissions without sacrificing performance.”
– Spokesperson for Allison Transmission
For example: Indianapolis-based Allison Transmission is designing medium and heavy duty truck transmissions with fuel economy as a priority. Using technology that optimizes shift timing based on load and terrain conditions, Allison’s automatic transmissions are better able to both save fuel, and apply acceleration power when needed. With the new transmissions, truck owners save an average of 5% in fuel and emissions, which rolls up to big savings for long haul tractor trailers. Other Allison technologies deliver even greater fuel economy improvements for buses and vocational vehicles. Discussing the company’s support for the EPA’s Phase 2 standards, a company spokeswoman recently said, “our latest technologies are already enabling our customers to reduce fuel consumption and emissions without sacrificing performance.”
Meanwhile Freightliner is using innovative Detroit Diesel engines, alongside Allison (and other innovative) transmissions in their increasingly fuel efficient trucks. Assembled in Mount Holly and Cleveland, North Carolina, Freightliner’s diesel and hybrid trucks also include technologies like new adaptive cruise control. This system combines GPS with digital mapping to adjust for the road ahead and create significant fuel savings. Through partnerships with universities and major commercial customers, Freightliner is developing trucks with fuel mileage twice the industry average.
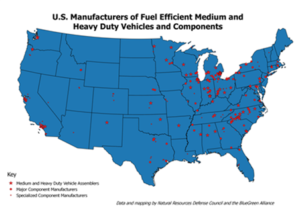
Research commissioned by the BlueGreen Alliance and NRDC in 2015 found several hundred facilities (shown here) and tens of thousands of workers making more fuel-efficient medium- and heavy-duty trucks and their components. A new study by the advanced truck industry group, CALSTART, finds 535 manufacturing and R&D sites making heavy duty vehicle high efficiency components and technology across the country.
Building a strong innovative network of suppliers matters for every technology
Sound long-term fuel economy standards have played a key role in rebuilding a strong, innovative network of automotive suppliers. No matter how automotive technology changes, job growth in America depends on sustaining a leading and globally competitive network of component manufacturers. Proterra, with manufacturing facilities in Greenville, South Carolina, and City of Industry, California, builds all-electric EV transit buses to meet increasing demand from municipalities across the nation who are looking at a variety of fuel alternatives both to save fuel costs and cut local air pollution. But Proterra is equally notable for its commitment to sourcing that technology in the United States. Its cutting edge EV transit bus is not only one of the most efficient on the market, but the company boasts 75 percent domestic content and that its electric bus includes components from 34 states.
Automotive manufacturing and the materials and components that go into it are at the heart of American manufacturing
Since the recession, the auto industry has brought back 700,000 direct jobs in motor vehicle and component manufacturing and at dealerships—jobs that, in turn, support several million jobs throughout the economy. But much more needs to be done. Continuing to lead globally and bring back good American jobs depends on sound fuel efficiency standards combined with strong manufacturing, labor, and trade policies. All across the country, hundreds of companies and tens of thousands of workers are building advanced trucks and the technology that goes into them. Let’s keep this momentum going.